350 mm Graphite Electrodes for 8 MW DC Furnaces: RS Group’s Expert Solutions. In the realm of electric arc furnace (EAF) technology, the right graphite electrode can make a significant difference in efficiency, productivity, and cost management. DC (Direct Current) furnaces, particularly high-capacity ones such as the 8 MW DC furnace, require electrodes designed to handle the intense electrical load and extreme temperatures inherent in the steelmaking process. RS Group, a leader in graphite electrode manufacturing, specializes in providing graphite electrodes tailored for various industrial furnace needs. One of our standout products is the 350 mm diameter graphite electrode, a perfect fit for the demands of an 8 MW DC furnace.
Recently, RS Group received an offer request for graphite electrodes from Marmara Metal, a well-known player in the metal industry. This request underscores the global demand for high-quality electrodes that meet the rigorous standards of modern furnace operations. In this blog, we will explore how RS Group’s 350 mm electrodes are ideally suited for 8 MW DC furnaces and why we are the preferred choice for companies like Marmara Metal.
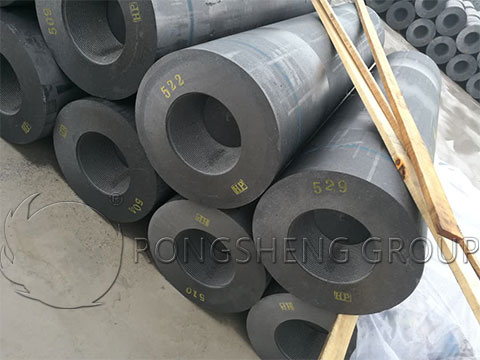
The Importance of High-Quality Graphite Electrodes in DC Furnaces
Direct Current (DC) furnaces have become increasingly popular in the steel industry due to their energy efficiency and lower environmental impact compared to Alternating Current (AC) furnaces. DC furnaces use a single graphite electrode, which carries the current from the power supply to the molten steel. This setup requires a durable, high-performance electrode capable of withstanding high electrical currents and extreme furnace temperatures.
Graphite electrodes serve as the critical component that transfers electrical energy into the furnace, creating the heat necessary to melt scrap metal or direct reduced iron (DRI) for steel production. The performance of these electrodes directly affects the efficiency of the furnace, the quality of the steel produced, and the operational costs of the process.
RS Group’s 350 mm graphite electrodes are designed to meet the specific needs of 8 MW DC furnaces, ensuring efficient electrical conductivity, thermal stability, and minimal wear during operation.
RS Group’s 350 mm Graphite Electrode: Ideal for 8 MW DC Furnaces
RS Group’s 350 mm diameter graphite electrode is engineered for heavy-duty applications, particularly in high-capacity DC furnaces. Here’s why it’s the perfect choice for an 8 MW DC furnace:
- Superior Electrical Conductivity: The 350 mm electrode is designed to handle the high current densities typical of DC furnaces. This ensures efficient energy transfer into the molten steel, reducing energy losses and shortening the melting cycle.
- Excellent Thermal Stability: DC furnaces generate immense heat, and RS Group’s 350 mm electrode is designed to maintain its structural integrity under extreme temperatures, often exceeding 3,000°C. This thermal resistance ensures consistent performance and reduces the risk of electrode failure.
- High Durability and Low Consumption Rate: Our graphite electrodes are crafted from premium-grade raw materials, such as needle coke, which offers low resistivity and high mechanical strength. This results in lower oxidation rates and a slower rate of wear, extending the electrode’s lifespan and reducing replacement costs.
- Compatibility with Furnace Operations: The 350 mm graphite electrode is perfectly suited for the electrical configuration of 8 MW DC furnaces, ensuring reliable performance and compatibility with existing equipment.
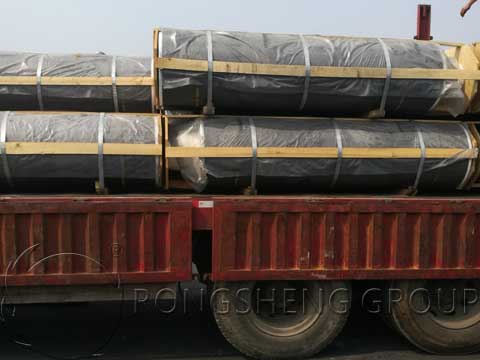
Responding to Marmara Metal’s Offer Request
Marmara Metal is a well-established supplier of raw materials and metals, serving industries across the globe. When companies like Marmara Metal submit offer requests for graphite electrodes, it’s a testament to the quality and reliability they expect from their suppliers. RS Group is proud to be among the top choices for such requests due to our reputation for delivering high-performance graphite solutions.
In response to Marmara Metal’s request, RS Group is well-positioned to supply the 350 mm electrodes required for their 8 MW DC furnace. We understand the specific needs of the steelmaking industry, where precision, durability, and efficiency are non-negotiable. Our electrodes undergo rigorous testing and quality control processes to ensure they meet the strictest international standards, including those required by Marmara Metal.
The RS Group Advantage: Meeting Global Demand
At RS Group, we have built a reputation as a trusted supplier of graphite electrodes for both AC and DC furnaces. Our manufacturing process combines cutting-edge technology with decades of experience in the industry, ensuring that our products meet the highest performance standards.
Key Features of RS Group’s Graphite Electrodes:
- Advanced Manufacturing Processes: We utilize state-of-the-art graphitization techniques to produce electrodes with uniform density, low resistivity, and high strength. This ensures that our 350 mm electrodes perform consistently under the high-stress conditions of an 8 MW DC furnace.
- Rigorous Quality Control: Every graphite electrode produced by RS Group undergoes a series of stringent tests for electrical resistivity, mechanical strength, oxidation resistance, and thermal stability. This rigorous process ensures that only the highest-quality electrodes reach our customers.
- Global Distribution Network: RS Group has established a global distribution network, allowing us to meet the needs of customers like Marmara Metal quickly and efficiently. Whether for domestic or international markets, we ensure timely delivery and reliable supply of our products.
- Customer-Centric Solutions: We understand that each customer has unique requirements. RS Group offers customized solutions tailored to the specific needs of our clients, ensuring that our 350 mm electrodes for 8 MW DC furnaces meet the exact specifications required for optimal furnace performance.
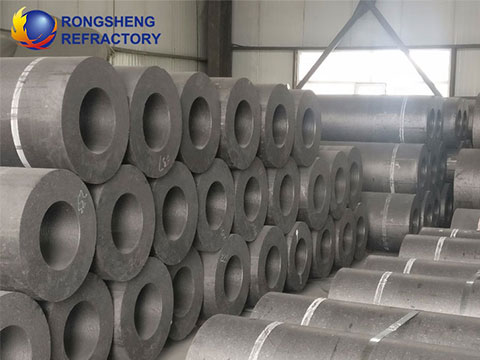
Applications of RS Group’s 350 mm Graphite Electrodes
RS Group’s 350 mm diameter graphite electrodes are widely used in a variety of industrial applications, including:
- Steelmaking in DC Furnaces: Our electrodes are designed to deliver consistent performance in electric arc furnaces, particularly in DC furnaces that require high-efficiency energy transfer for melting scrap and DRI.
- Non-Ferrous Metal Smelting: The thermal stability and durability of our 350 mm electrodes make them ideal for smelting non-ferrous metals such as copper, aluminum, and nickel.
- Ferroalloy Production: In ferroalloy production, the high temperatures required for melting alloys demand electrodes that can withstand extreme conditions. RS Group’s electrodes are up to the task, providing the necessary conductivity and durability for these processes.
RS Group Graphite Electrodes Commitment to Quality and Performance
RS Group is committed to providing high-quality graphite electrodes to meet the growing global demand for reliable furnace solutions. Our 350 mm diameter electrodes are designed to handle the rigorous demands of 8 MW DC furnaces,
ensuring efficiency, durability, and cost-effectiveness in steelmaking and other high-temperature industrial processes. As a trusted supplier, RS Group is proud to respond to offer requests from industry leaders like Marmara Metal, delivering customized graphite solutions that meet the highest standards. With our advanced manufacturing techniques, rigorous quality control, and commitment to customer satisfaction, RS Group is the ideal partner for companies seeking high-performance graphite electrodes for demanding furnace operations.