In the production of yellow phosphorus produced by the electric furnace method, the consumption of graphite electrodes includes two parts: the normal consumption used to generate electric arc to supply electric energy to melt the charge and participate in the main reaction of reducing phosphorus and iron, and abnormal consumption caused by electrode breakage or other factors. The latter is related to the quality of the electrode. To sum up, in the production of yellow phosphorus produced by the electric furnace method, there are five types of abnormal consumption of graphite electrodes: oxidation, sublimation, absorption, cracking-off, and creasing, etc. How to reduce the abnormal consumption of electrodes to reduce costs, deal with various abnormal problems in production in time, and keep the electric furnace running smoothly are issues worthy of discussion in production.
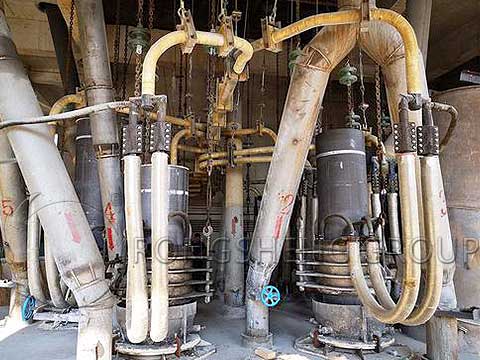
Oxidation Consumption of Graphite Electrodes
The process in which graphite reacts with oxygen at high temperature to form CO or CO2 is called oxidation consumption. Oxidation consumption occurs on the surface of the electrode, and in severe cases, it will shed and delaminate. The yellow phosphorus electric furnace is in a strongly reducing environment during normal operation. Oxidation consumption is very small, only a small amount of oxidation consumption in electric ovens (especially open ovens), but it is mainly caused by high-temperature convection gas. Therefore, in the electric oven, the furnace must be strictly inspected to seal the leak points that are prone to air convection.
Evaporation Consumption of Graphite Electrode
Graphite is gaseous at high temperatures, and the process of leaving the surface to escape is called evaporation consumption. It usually appears at the lower end of the electrode. Excessive current is the culprit leading to evaporation. In other words, the evaporation phenomenon is even worse under a strong current. Therefore, excessive use of strong current should be avoided in production, and the intensity of electrode current must be controlled to reduce and radically eliminate evaporation. The general requirement is to control the three-phase electrode terminals to do work on the same plane.
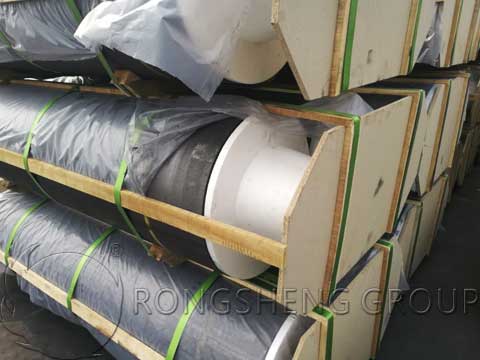
Absorption Consumption of Graphite Electrode
The process of graphite electrode melting into the slag melt at high temperature is called absorption consumption. Electrode immersion and short arc are the main reasons for the increase in absorption consumption. If the dipping operation is performed, the electrode end will chemically react with iron, calcium oxide, and other substances in the slag to produce iron carbide, calcium carbide, etc. The reaction formula is:
C + Fe — FeC OR nC + mFe — FemCn
3C + CaO — CaC2 + CO↑
Calcium carbide will further react with carbon and silica in the slag to form calcium silicide. The reaction formula is:
CaC2 + 2SiO2 + 2C — CaSi2 + 4CO↑
A short arc will also accelerate the evaporation of the electrode tip. At this time, the graphite is in a gaseous state, and the above reaction also occurs when the arc sprays into the molten slag. Therefore, short arc and flooding operations must be reduced or eliminated in production control to avoid this situation.
Exfoliation Consumption of Graphite Electrode
The phenomenon of electrode cracking and separation caused by temperature difference or other reasons is called exfoliation and consumption of graphite electrode. “Peeling” easily occurs at the tip of the electrode. There are two reasons: (1) the quality of the electrode itself. (2) Peeling during operation.
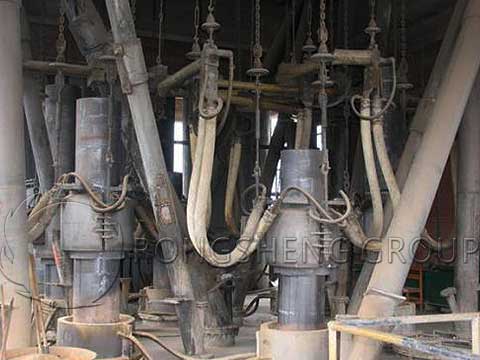
Broken Consumption of Graphite Electrode (also called Breakage)
Broken consumption refers to the consumption caused by the electrode being broken by the impact of radial force. It can be discussed in two parts.
Damage caused during use
- (1) The joint area is damaged. It can be seen from some examples of damage to the joint area that it is caused by loose tripping.
- (2) Electrode connection and dust removal. The connecting part of the electrode is precisely processed before leaving the factory. If there is dust or carbon dust during storage and transportation, and it is not processed during use, it will cause gaps in the joints. As a result, the local temperature of the electrode is increased, and the layer is oxidized and delaminated, which weakens the mechanical strength and causes the electrode to be broken.
- (3) Clamping of electrodes. When changing the electrode holder, if it is clamped outside the threaded hole area of the electrode, it will cause the electrode threaded hole to crack and cause breakage.
- (4) Storage of electrodes. The storage and custody of the electrode should be in a dry and ventilated warehouse. Don’t get damp or moldy spots. Once a damp or moldy beard is found, use it after drying. The damp electrode will burst into the furnace and cause breakage.
Damage caused by other factors
- (1) Insufficient concentricity of the electrode hole, water seal device, lifting device, etc. on the phosphor furnace cover, or the center of the three electrodes deviates from the center circle, will cause the breakage of the graphite electrode. Therefore, in the production and installation (or overhaul), a comprehensive assessment is required to strictly complete the design requirements.
- (2) Factors such as excessive particle size of the furnace charge, unsuitable ingredient ratio, more powder, high moisture content, and uneven feeding will cause the furnace to run unsmoothly. It causes hanging materials and sheds, and then collapses again, causing a radial impact on the electrode and breaking it. If the above-mentioned hidden dangers occur in the phosphorus furnace, the quality of raw materials and charging methods must be improved immediately. As long as we observe and operate frequently, strictly control various process indicators, and keep the furnace running smoothly at all times, the electrode breakage caused by such situations will be reduced or eliminated.
- (3) If the electrode shakes too much during the lifting process, it is easy to cause the joint to loosen, snapback, or break. At this time, the reason should be found and the balance should be adjusted so that the electrode no longer shakes during lifting.
- (4) When the slag is discharged, the electrode is not moved down enough, and the charge slips into the lower end of the electrode, and the oblique radial component force generated causes the electrode to break. Or because the electrode circuit is cut off, a two-phase operation is formed. If measures are not taken in time to remedy it, the electrode will be broken.
- (5) Water-sealed water leaks into the electrode or copper tile electrode clamp, and sparks when it comes into contact with the electrode. If not detected in time, sparks will increase and the chuck water jacket will burn through and leak water, which will cause electrode breakage.
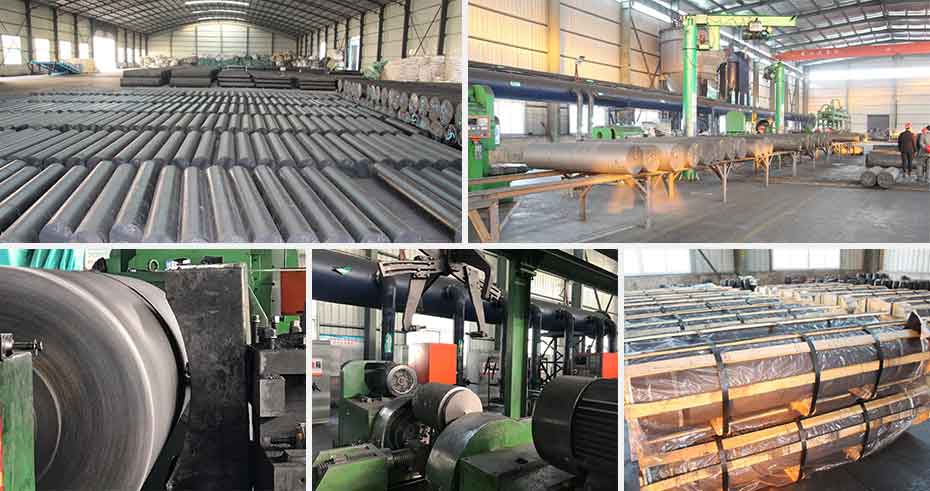
In summary, in the preparation of yellow phosphorus by the electric furnace method, as long as the cause of abnormal consumption of graphite electrodes is understood, appropriate countermeasures can be selected to overcome it. In order to reduce and eliminate the abnormal consumption of graphite electrodes. Deal with all kinds of abnormal problems in time and keep the furnace running smoothly to reduce or prevent abnormal consumption of graphite electrodes. Learn more from the graphite electrodes manufacturer.