The graphite electrode blank after graphitization is machined according to the shape and size specified by the quality standard. The graphite electrode body and nipples that meet the requirements of use are made.
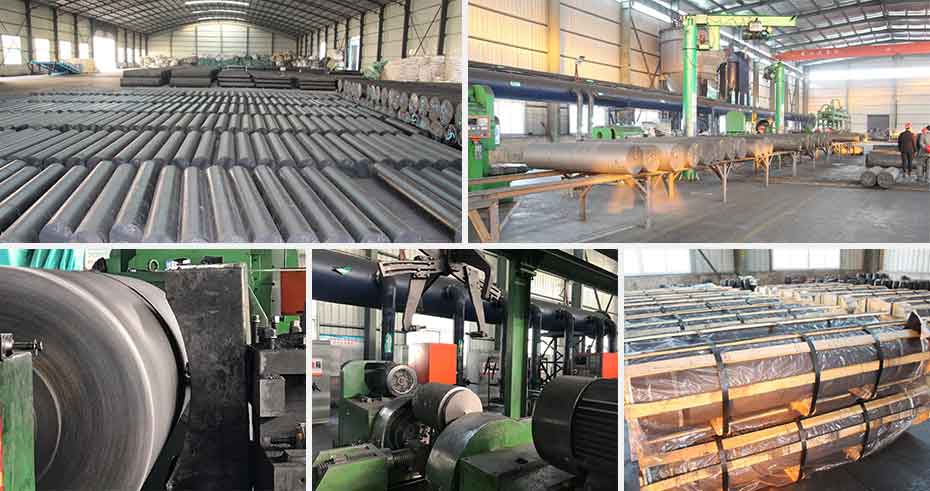
Processing Equipment for Graphite Products
Graphite electrode processing is divided into two independent processing parts, the electrode body and the joint. Electrode body processing includes three unit operations: car outer circle, end surface processing (flat end surface and boring screw hole), processing connection thread (female thread), and half button in the screw hole. Joint processing includes three unit operations: turning the outer circle, processing the male thread on the outer surface, grinding the two end faces after cutting, and processing the half button.
Use ordinary lathe for processing. Electrode body processing generally consists of 3 lathes to form an assembly line. The first lathe is responsible for external machining, the second lathe is responsible for processing the end face and boring, and the third lathe is dedicated to processing the threads in the screw holes.
The joint processing is generally completed by two other lathes. The first lathe is responsible for external machining and milling of male threads on the surface, and a deep groove is cut to the specified length (not broken). The second lathe processes the two end faces and half buckles of the joint after the disconnection (small size products can be processed by a grinder).
The processing of joints, turning the outer circle, and milling male threads are the same as the processing of the electrode body. The flat end face and processing half of the large-size joint are carried out on the lathe.
The main disadvantage of using ordinary lathe processing is that the processing quality is unstable. Because the electrode blanks are heavier and bulkier, for example, the length of a graphite electrode with a diameter of 500 mm is up to 2 m, and each weighs about 500 kg. In addition, the geometry of the electrode blank is not uniform, with bending and deformation. Ordinary metal cutting lathes are not rigid enough. Therefore, periodic vibration occurs when the chuck of the lathe clamps the blank and rotates. The higher the speed, the greater the vibration. It is impossible for the outer circle, end face, and thread processed under this vibration state to achieve high precision. The rough shape with larger defects cannot completely eliminate bending and deformation after processing. The screw holes at both ends of the electrode may not be concentric with the outer circle, the verticality of the trunk and the end face will have deviated, the screw thread and the fit-gap error will be large, and the processing efficiency is relatively low.
Use specially designed modular machine tools for processing. Graphite electrode is a mass-produced product, and there are not many actions required for processing. Therefore, it is possible to design and manufacture special and efficient modular machine tools.
Characteristics of Graphite Products Processing
The processing of graphite products has the following 5 characteristics.
(1) Graphite products are different from metal materials and wood. It is a heterogeneous brittle material. The hardness is not high, it is easier to cut, and can be processed into products with higher precision and different shapes. However, due to the difference in product volume density and graphitization degree, the hardness of graphite products fluctuates in a considerable range.
(2) Graphite products are non-homogeneous brittle materials. Therefore, graphite particles of different sizes are generated during cutting, instead of band-shaped chips when cutting metal materials.
(3) A certain amount of cutting heat is also generated when cutting graphite products, but there is no need to use coolant or protective lubricating fluid on the machined surface. When cutting graphite products, a certain shock and vibration will be generated, so generally high-speed steel or cemented carbide tools with better shock and vibration resistance are used.
(4) A large amount of dust is generated during the cutting process. Not only pollutes the environment, but also affects the health of operators. In addition, there are some impurities such as silicon carbide in the graphite dust that cause certain wear on machine tool components. Therefore, the machine tool cutting graphite products must be equipped with ventilation and dust removal equipment.
(5) Although graphite products are a brittle material with low hardness, the wear on the cutting edge at low-speed cutting is more serious than when cutting cast iron. If the carbide tip is selected and the cutting speed is 80 m/min, the continuous use time of the blade when cutting the graphite electrode is generally only about 200 min. The cutting edge needs to be sharpened, and it can reach more than 600 minutes when cutting cast iron. For cast iron, the lower the cutting speed, the more beneficial it is to extend the continuous use time of the blade. The opposite is true for cutting graphite electrodes. High-speed cutting is appropriate. Multi-tool and multi-edge turning and milling techniques are often used to process graphite electrodes.