In steel mills, the consumption of furnace electrodes are mainly broken consumption. How does such consumption of furnace electrodes occurs during the steelmaking process? According to the summary of experienced steel mills, there are roughly the following factors that lead to the broken of graphite electrodes in the steelmaking process.
- The electrode arm is tilted. The furnace electrodes crossarm are not correct, which will cause the electrode to tilt. When the electrode is moved, it “collides” with the refractory brick, causing the furnace electrode to be broken. The electric arc furnace is operated in the environment of high temperature, dust and corrosive gas all year round, and the parts are easily oxidized and deformed.
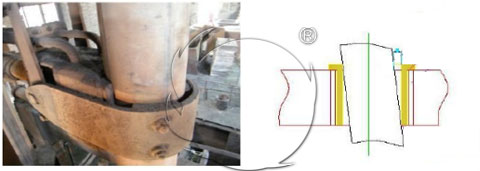
- The electrode hole is exposed to high temperature for a long time, and water leakage will occur. After many times of repair welding, deformation will occur. Misalignment of the refractory bricks in the electrode holes causes the electrodes to “collide and fight” with the refractory bricks. Thereby breaking.
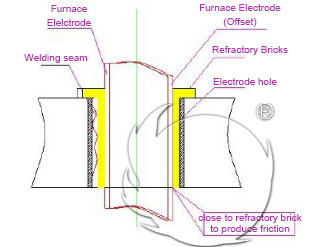
- When the inner hole of the gripper is not smooth and uneven, electrode flashing may occur. In severe fires, the electrodes will be interrupted. This phenomenon is very common in the steelmaking production process.
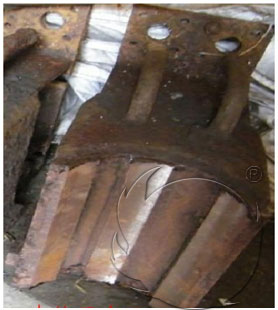
- The impact and vibration of the arc make the electrode joints loose. Steelmaking operations at night, the scene of heavy smoke and dust. The on-site lighting is not enough, which affects the foreman to observe the loose electrode.
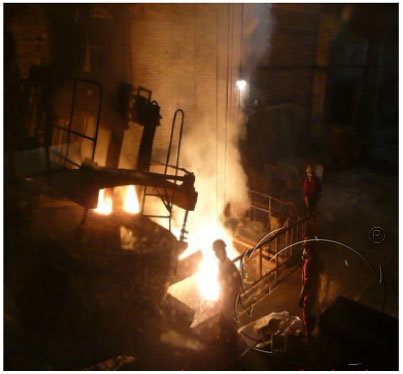
In addition, there are some excluded factors. For example, the quality of furnace electrodes is unqualified, the connection between the electrodes and the joints is not close, the long-term tilt operation of the electric furnace, human factors, etc., can also cause the furnace electrodes to break.
As a graphite electrode supplier, we promise that our graphite electrode products are of reliable quality and guaranteed. We do not provide products with unqualified furnace electrodes for electric arc furnaces.