As we all know, graphite electrodes use petroleum coke and needle coke as aggregates and coal pitch as the binder. Production Process of Graphite Electrodes, through a series of processes such as kneading, forming, baking, impregnation, graphitization, mechanical processing, etc., a high-temperature resistant graphite conductive material is produced. Its price is also on the market. It has different characteristics in different periods, which also affects the cost of electric arc furnace steelmaking production.
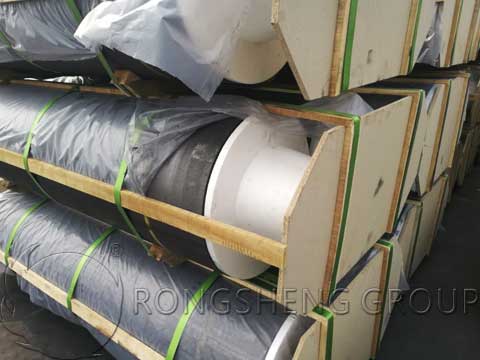
Uses of Graphite Electrodes
Graphite electrode is an important high-temperature conductive material for electric furnace steelmaking. The graphite electrode is used to input electric energy into the electric furnace, and the high temperature generated by the arc generated between the electrode end and the charge is used as the heat source to melt the charge for steelmaking. Some other submerged arc furnaces for smelting yellow phosphorus, industrial silicon, abrasives, and other materials also use graphite electrodes as conductive materials. Utilizing the excellent and special physical and chemical properties of graphite electrodes, it is also widely used in other industrial sectors.
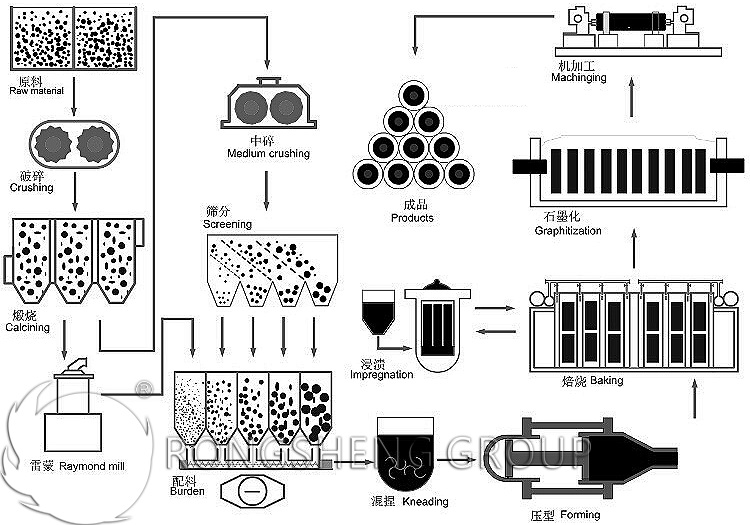
The Production Process of Graphite Electrodes is as Follows:
- Calcined. Both petroleum coke or pitch coke needs to be calcined. The calcination temperature should reach 1350°C. The purpose is to fully remove the volatile matter contained in the carbonaceous raw materials and improve the true density, mechanical strength, and conductivity of the coke.
- Crushing, screening, and batching. The calcined carbonaceous raw material is crushed and sieved into aggregate particles of a specified size. Part of the coke is ground into fine powder, weighed according to the formula, and aggregated to form a dry mixture of various particles.
- Kneading. Under the heating state, the quantitative dry mixture of various particles and the quantitative binder are stirred and mixed and kneaded to form a plastic paste.
- Forming. Extrusion molding under external pressure; or vibration molding under high-frequency vibration. The paste is pressed into a green electrode green body with a certain shape and higher density.
- Baking. Place the green electrode in a special baking furnace, and use metallurgical coke powder to fill and cover the green electrode. At a high temperature of about 1250°C, the binder is carbonized to form coke. Thus, a fired carbon electrode was prepared.
- Impregnation. In order to improve the density and mechanical strength of the electrode product, the fired electrode is installed in the equipment. After immersing the liquid impregnant pitch electrode into the pores, a second roasting should be carried out. According to product performance requirements, sometimes impregnation and secondary roasting need to be repeated 2 to 3 times.
- Graphitization. Put the roasted carbon electrode into the graphitization furnace and cover the insulation material. The carbon electrode is converted into a graphite electrode with a graphite crystalline structure at a temperature of 2200~300°C using a heating method that generates high temperature by direct energization.
- Machining. According to the application requirements, the graphite electrode blank is surface turned, the flat end face and the screw hole for connection are machined. At the same time, the joints for connection are processed.
The production process of graphite electrodes is complicated and the production cycle is long. Graphite electrode manufacturers also strictly control the quality of graphite electrodes. The purpose is to save production costs. To get the UHP graphite electrode quotation, you can contact us by email or submit the form on our page. Look forward to working with you.