The evolution of steelmaking has seen remarkable advancements over the years, driven by technological innovation and the increasing demand for high-quality steel products. One of the most critical components in this process is the Ultra-High Power (UHP) graphite electrode. The Critical Role of UHP Graphite Electrodes in Modern Steelmaking. These electrodes are essential in electric arc furnace (EAF) steelmaking, which accounts for a significant portion of global steel production. Among the various types of UHP graphite electrodes, two stand out for their specialized applications: the UHP Graphite Electrode UHP 500×2400 mm and UHP graphite electrodes with a nipple diameter of 350 mm.
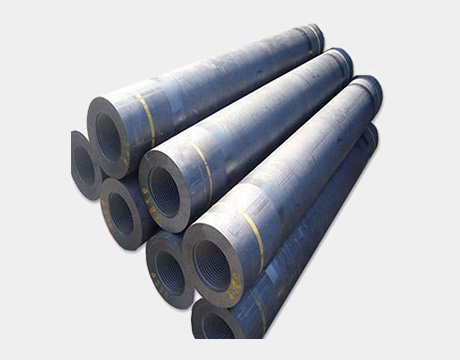
The Significance of UHP Graphite Electrode UHP 500×2400 mm
Among the various sizes of UHP graphite electrodes available, the UHP Graphite Electrode UHP 500×2400 mm is particularly noteworthy. This specific size is designed for large-capacity EAFs, which are used in high-volume steel production. The dimensions, 500 mm in diameter and 2400 mm in length make this electrode ideal for heavy-duty applications, where high power input is required.
The larger diameter and length of the UHP 500×2400 mm electrode provide several advantages. First, the increased surface area allows for better heat dissipation, reducing the likelihood of thermal damage and extending the electrode’s lifespan. Second, the larger size enables higher current-carrying capacity, which is essential for maintaining consistent and efficient steel production. This makes the UHP 500×2400 mm electrode a preferred choice for steelmakers aiming to optimize their operations and minimize downtime.
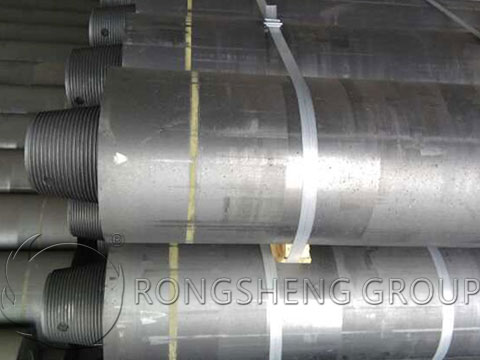
Understanding UHP Graphite Electrodes
UHP graphite electrodes are primarily used in electric arc furnaces (EAF) for steelmaking, where they conduct electrical energy to melt scrap metal and convert it into liquid steel. These electrodes are known for their ability to withstand extremely high temperatures, high electrical conductivity, and resistance to thermal shock, making them indispensable in the EAF process.
The term “Ultra-High Power” refers to the electrode’s ability to handle extremely high current densities, typically exceeding 25 A/cm². This is crucial in modern steelmaking, where efficiency and productivity are paramount. UHP graphite electrodes are made from high-purity petroleum coke and needle coke, which are processed through a series of steps, including calcination, milling, and graphitization, to produce a highly conductive and durable product.
Exploring UHP Graphite Electrodes with Nipple Diameter: 350 mm
Another critical variant of UHP graphite electrodes is the one with a nipple diameter of 350 mm. The nipple is a crucial component of the graphite electrode, serving as the connector between multiple electrodes to form a continuous column. The diameter of the nipple plays a significant role in the overall performance and stability of the electrode column.
A 350 mm nipple diameter is typically used in medium to large EAFs, where robust mechanical and electrical connections are essential. The larger nipple diameter enhances the mechanical strength of the connection, reducing the risk of breakage during operation. Additionally, it improves the electrical conductivity between the connected electrodes, ensuring a stable and efficient flow of current.
The design and manufacturing of UHP graphite electrodes with a 350 mm nipple diameter are highly specialized processes. These electrodes undergo rigorous quality control to ensure that the nipple and electrode body have optimal compatibility, minimizing the risk of joint failure. This level of precision is crucial in maintaining the integrity of the electrode column during high-temperature and high-current operations.
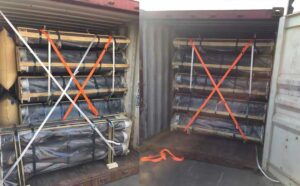
The Role of Quality Control and Innovation
The production of UHP graphite electrodes, particularly the UHP 500×2400 mm and those with a 350 mm nipple diameter, involves stringent quality control measures. Manufacturers must ensure that the raw materials, such as petroleum coke and needle coke, are of the highest quality. Any impurities in these materials can compromise the performance of the electrodes, leading to operational inefficiencies and increased costs for steelmakers.
Innovation in the production process is also key to enhancing the performance of UHP graphite electrodes. Advances in material science and manufacturing techniques have led to the development of electrodes with improved thermal and electrical properties. For example, the use of advanced graphitization processes can enhance the uniformity and density of the electrode, leading to better performance and a longer lifespan.
The UHP Graphite Electrode UHP 500×2400 mm
UHP graphite electrodes are a cornerstone of modern steelmaking, enabling efficient and high-volume production of steel. The UHP Graphite Electrode UHP 500×2400 mm and UHP graphite electrodes with a nipple diameter of 350 mm are two specialized variants that play a critical role in this industry. Their unique dimensions and design features make them indispensable in large-capacity and high-temperature applications, where performance and durability are paramount.
As the demand for high-quality steel continues to grow, the importance of UHP graphite electrodes will only increase. Steelmakers and electrode manufacturers must continue to invest in research and innovation to develop electrodes that meet the evolving needs of the industry. In doing so, they will ensure that UHP graphite electrodes remain a vital component in the production of steel, driving progress and supporting global industrial growth.