With the modern development of iron and steel smelting technology, the safety and economy of the use of Graphite Electrodes and Electrode Nipples in steel mills have become increasingly prominent. So how to realize the ideal connection between the graphite electrode and connector? Based on its high precision, someone proposed a new concept of an “ideal connection” between graphite electrode and electrode nipple. If the “ideal connection” between the electrode and the joint can be realized, the risk of burning and loosening during use will be greatly reduced. It can also partially compensate for the impact of insufficient strength caused by material defects. And significantly reduce power and material loss, thereby improving economic benefits.
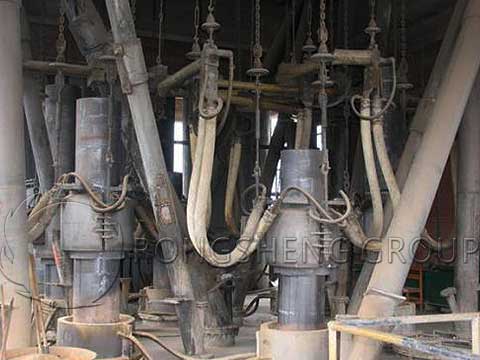
“Skin effect” is the theoretical basis for the “ideal connection” between graphite electrode and electrode nipple
Helmut Willstedt, a famous German carbon expert, pointed out in the book “Basic Principles of Graphite Electrode Production, Inspection, and Application”: “About 80% of the current of graphite electrode and electrode nipples in use flows through the electrode end faces. .”
This passage comes from the fundamentals of electricity. That is to say, in the process of current conduction, 80% of the current flows through the largest diameter of the conductor, which is the so-called “skin effect”. The electrodes and connectors are also electrical conductors during use, so the “skin effect” is also applicable. So, what does the “skin effect” have to do with the “ideal connection” of electrodes and connectors?
There is no doubt that the “skin effect” is extremely beneficial to the use of electrodes and connectors.
First of all, due to the “skin effect”, about 80% of the current of the electrodes and connectors flows through the electrode end faces during use. However, if the electrode end faces are in contact with a large area, the contact resistance is very small. Therefore, the power consumption is greatly reduced, which can reduce the unit electrode loss of smelting enterprises and improve economic benefits.
Second, only 20% of the electrical current of the electrodes and connectors flows through their threaded connections during use. Compared with the traditional electrode end face without contact or poor contact, 100% current flows through the threaded connection, the power consumption is reduced by more than 80%, and the heat generation is greatly reduced. It can eliminate the phenomenon that the traditional graphite electrode and electrode nipple threaded joints are burnt at a high temperature due to high current and thus broken. However, the existence and function of the “skin effect” are conditional. The conditions are as follows.
- (1) The contact rate of the electrode end surface is close to 100%, and the current-carrying area is maximized, especially since the contact at the largest diameter of the electrode is good. This is the basis for the existence of the “skin effect”. If this condition cannot be achieved, the current can only pass through the threaded connection because the electrode end faces are not in contact or in poor contact when energized. Its “skin effect” can only be the “skin effect” at the largest diameter of the threaded connection, and the conduction resistance and power consumption will be greatly increased.
- (2) The relevant precision of the threaded connection is well-matched, and the connection is tight and reliable. It not only minimizes the resistance and heat generation when 20% current passes but also ensures good contact with the end faces.
The connection between the electrode and the connector that meets the above two conditions is the “ideal connection”.
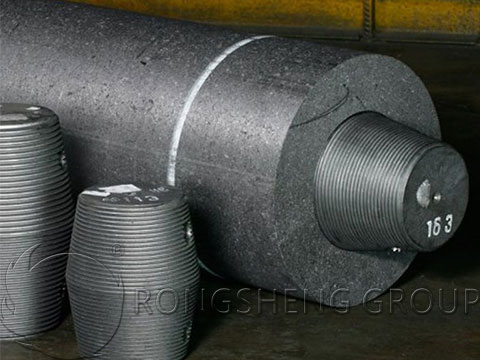
Processing requirements to realize the “ideal connection” between graphite electrodes and nipples
First of all, from the analysis of the above item (1), in order to achieve the contact rate between the graphite electrode and electrode nipple end surface approaching 100%, the processing of the end surface of the graphite electrode must meet the following requirements.
- (1) The height of the electrode end face is flat, and the flatness error is ≤0.012mm.
- (2) The end surface of the electrode must not be convex, but only concave, and the concave amount is ≤0.05mm.
- (3) The verticality error between the electrode end surface and the thread center line is ≤0.01mm.
- (4) The 4-point deviation between the electrode and the nipple thread is ≤0.04 mm.
Secondly, from the analysis of the above condition (2), in order to achieve a good matching of the relevant accuracy of the threaded connection and a tight connection, the machining accuracy must meet the following requirements.
- (1) The single thread pitch error is ≤0.012 mm, and the cumulative pitch error is ≤0.03 mm/152.4 mm. In this way, each thread of the connecting thread can be tightly and evenly matched.
- (2) The thread diameters of the electrode and connector are (d + 1/2 t), + 0.03 ~ 0 mm, and (d + 1/2 t), 0 ~ -0.03 mm, respectively. Among them, t is the guaranteed gap value in the diameter direction according to the thermal expansion coefficient of the graphite electrode and electrode nipple material and experience. When it is not energized, the screw teeth are well connected, and it will not be crushed and burned due to expansion after energizing and heating.
- (3) The bevel angles of the electrode and joint threads are 9°27’44″(+5″ ~ -1′) and 9°27’44″(+1′ ~ -5″), respectively. After connection, the contact of the big end is relatively hard, and the contact of the small end is soft, so the bearing capacity is large.
- (4) The thread half angle is 30°±10′, and the tooth surface roughness Ra≤3.2μm. In addition, the staggered amount of the outer diameter of the connection between the electrode and the joint must be ≤0.15 mm to prevent pinch-off when clamping and energizing. Therefore, the coaxiality between the centerline of the electrode thread and the outer circle is required to be ≤0.07 mm.
Obviously, the “ideal connection” of graphite electrodes and electrode nipples puts forward many requirements beyond the conventional ones for machining accuracy. When encountering problems that are difficult to solve with traditional processing technologies, high-precision processing is the only way to go.
Rongsheng is a high-quality graphite electrode supplier. Contact us for a free trial.