The reliability of graphitized electrodes in electric arc steelmaking furnaces, in many cases, depends on their ability to resist thermal stress. The final effect of thermal stress depends on the size and nature of graphite deformation.
Regarding the deformation properties of graphite electrodes, the research is insufficient. Because people have focused their attention on the mechanical strength related to the reliability of electrode products. If the relationship between deformation and stress-linear elasticity is considered to be a linear relationship, it is appropriate to do so. However, the deformation curve of the graphite electrode is not linear from the initial load. The deformation of the graphite electrode includes an elastic component and an inelastic component. Under thermal load conditions, the effect of the inelastic component is great. The inelastic force of graphite-type materials (composites, ceramics, refractory materials, etc.) with small deformation will increase the reliability of the thermal load structure.
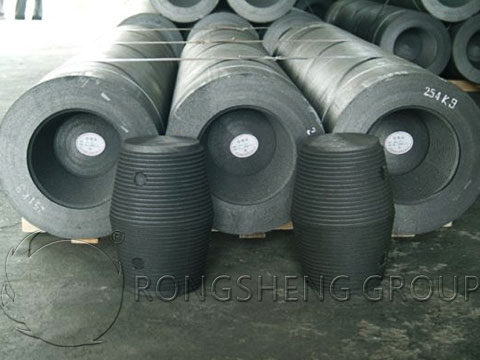
As we all know, the mechanical properties of graphite are closely related to its structural parameters. Under the conditions of changing the original aggregate particle size, graphite porosity, and heat treatment temperature, a series of graphites with different mechanical strengths, Young’s elastic modulus and shear elastic modulus can be prepared. However, the relationship between the deformation of graphite electrodes and process factors has not been studied. Moreover, this relationship cannot be judged by the magnitude of elastic modulus and strength limit value. Because the relationship between them is not linear.
Therefore, it is of great significance to evaluate the possibility of deformation of graphite electrodes by purposely changing the production process of graphite electrodes.
This article is based on the known assumption that the material macrostructure heterogeneity and the microstructure ordering play a decisive role in the formation of the inelastic component.
The macroscopic heterogeneity of graphite is defined by the fluctuation of the material density, the different orientations and values of the structural units, and the presence or absence of pores with different sizes, shapes, and orientations.
The process factor that has the greatest influence on the heterogeneity of the macrostructure of the graphite electrode is the polydispersity particle size composition of the aggregate coke.
The particle size composition of aggregate coke largely determines the porosity and properties of graphite, as well as the size and shape of most pores.
Carbon products impregnated and roasted with coal pitch can also achieve the purpose of changing their porosity and heterogeneity. After asphalt impregnation, the pores of the product are partially blocked, so that the total porosity is reduced.
The main factor affecting the perfection of the microstructure is the final temperature of the heat treatment. Increasing the graphitization temperature can increase the perfection of the graphite lattice.
This article discusses the process factors that cause graphite heterogeneity and affect its deformation. The aggregate coke particle size composition, pitch impregnation, and graphitization temperature were discussed.
The sample is pressed with a paste of K3-8 calcined petroleum coke and coal tar pitch, with a diameter of 60 mm. It is roasted to 1373K in a chamber furnace, and the heating rate is 30K/h. Buried in filler at 2773K for graphitization.
The deformation of graphite is determined according to the deformation diagram obtained when a cylindrical specimen with a diameter of 15 mm is stretched (measurement standard 80 mm). The deformation properties and inelasticity of graphite are shown in Figure 1. Deformation is determined at the point on the deformation diagram that corresponds to the failure of the specimen. The particle size composition of the material is changed by increasing the large particles and reducing the small particles.
As the average particle size of the dry material increases from 0.79 to 1.26mm, the heterogeneity of graphite increases, and the porosity increases.
Although the tensile strength is reduced, the total deformation value does not actually change. In this case, the nonlinearity of graphite deformation is significantly improved (1.3 times).
The macrostructure of graphite will also change even after the blank is immersed after firing. For example, the porosity of graphite has dropped from 30.2% to 25.2%. The tensile strength is now increased by 0.9 times.
Due to the significant increase in strength, the total deformation rate of graphite has increased from 0.11% to 0.14%. However, reducing the porosity of graphite and increasing the density reduces the inelasticity from 0.2% to 0.15%.
On the samples with the same macrostructure and the firing temperature up to 1075K, the influence of the maximum heat treatment temperature was studied.
When the heat treatment temperature is increased to 2473K, the mechanical strength of graphite is significantly reduced. However, the total deformation and inelasticity of graphite do not actually change.
When the heat treatment temperature exceeds 2673K, the inelasticity of graphite is significantly increased. It should be noted that despite the decrease in strength, the total deformation of the graphite material is still greater than that of the fired material (1073K). The inelastic deformation of graphite is 19~46% of its total deformation, which has a wide range of variation.
When the graphite size increases and the heat treatment temperature increases, its deformation inelasticity is very large, but when the graphite electrode blank is impregnated and roasted with pitch, its deformation inelasticity decreases. Therefore, it is possible to purposely change the process parameters to produce graphite electrodes whose deformation properties meet the requirements.