In the production of carbon products in a certain period of time, Shengli coke with high sulfur content is used as raw material in a considerable proportion. These cokes have the characteristics of high volatile content, high sulfur content, and difficult graphitization. It is difficult to control the production process, so the product is prone to cracking, which affects the yield and economic benefits. Therefore, the use of these coke to produce high-quality products has become a problem worthy of study in the production of carbon products in my country.
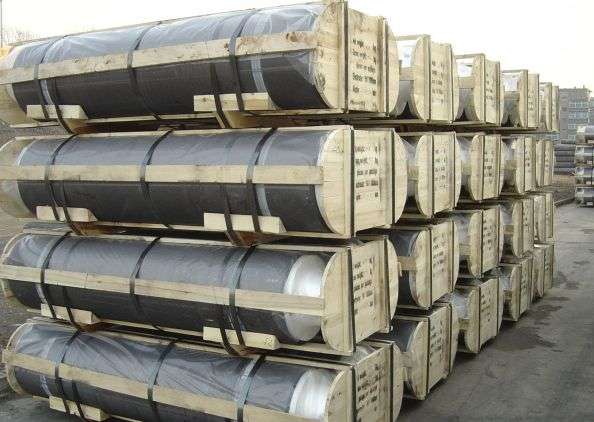
How to Improve the Quality of Graphite Electrodes?
It is indeed difficult to use petroleum coke with high sulfur content to produce graphite electrodes. When Shengli coke started to use, a lot of cracked waste products were produced. Especially in the graphitization process, there are many cracks in graphite electrode products. Individual heats reach 50~60%, which seriously affects economic benefits. According to the actual production situation, after research, the factory decided to take the following measures in the process.
First, increase the calcination temperature as much as possible to discharge some organic sulfur.
Increase the calcination temperature to 1300~1350℃ to eliminate volatile matter and a part of organic sulfur, so that the coke volume can reach the maximum shrinkage. In order to reduce the volume shrinkage during the heat treatment in the subsequent process.
Second, adding iron oxide powder to the coke suppresses the “swelling” effect of sulfur and can play a role in catalyzing graphitization.
Using the above measures, a manufacturer conducted a production test to confirm the role of iron oxide in the production of graphite electrodes. During the test, the traditional product without iron oxide and the test product with iron oxide (both φ300 electrodes) were entered into the process production line for comparison tests. The test product was added with 0.6-1.0% Fe2O3 powder in the formula, the purity of which was 97.1%, and the particle size was less than 200 mesh.
According to the test data, this manufacturer has drawn the following conclusions through analysis. The cracks of the test product were significantly reduced, and the yield rate was significantly improved. The average yield rate of the four furnaces of the traditional product was 57.05%, while the yield rate of the two furnaces of the test product was 93%. From the perspective of physical and chemical indicators, the true density and bulk density has increased to varying degrees, the porosity has decreased, and the ash content has increased slightly.
After the test is successful, adding iron oxide to produce graphite electrodes has become an important measure in the production process. Supervise and guarantee the addition amount and uniformity through laboratory analysis of the paste.
How to Add Iron Oxide Powder Evenly?
The iron oxide powder used by the graphite electrode manufacturer has a Fe2O3 content of more than 98%, a particle size of less than 200 mesh, and a certain proportion of finer particles. When starting to use Fe2O3, add 0.6-1.0% of the total weight of the paste directly into the batching cylinder, and then enter the kneading pot for dry mixing. Through a period of practice, it has been proved that the mixing is not uniform. Sometimes it is difficult to knead the iron oxide powder when it is damp, and small iron powder lumps are found on the section of the green body and the fired product. In this way, pores are easily formed after graphitization, and at the same time, they cannot play their due role. Therefore, it was later added to the ball mill.
A small disc feeder or a small electromagnetic feeder is installed on the screw feeder of the ball mill, and a hopper is connected to it, and the iron oxide powder is loaded into the hopper. After the ball mill is started, adjust the feeding speed of the coke to control the feeding amount, and then start the iron oxide powder feeder. After the iron oxide powder enters the ball mill evenly, it is thoroughly mixed with the coke powder and further finely divided at the same time. Those small pieces formed by the tide were also crushed at the same time. In the ingredients, the powder of various particle sizes enters the kneading pot at the same time, and the dry mixing is basically uniform for 20 minutes. In the green electrode produced in this way, the distribution of iron oxide powder is relatively uniform.
For several years, the graphite electrode manufacturer has insisted on using this process for production. The crack phenomenon of the electrode is basically controlled, and the ash content is also reduced to within the national standard value. Product quality continues to rise, and output is also increasing year by year. The graphite electrodes produced have been used in steel plants for many years, and the effect has been very good. The consumption of steel per ton is below 6.5kg/t steel.
To learn more about the product knowledge of graphite electrodes, please continue to pay attention to us.