Graphite Electrodes for Electric Arc Furnace are conductor material that the electric arc furnace releases electric energy in the form of an electric arc to heat and melt the charge. Due to the extremely harsh working environment, compared with other conductive materials, graphite electrodes have some excellent or irreplaceable characteristics under high-temperature conditions. For example, its strength increases with increasing temperature, and its thermal expansion coefficient is low.
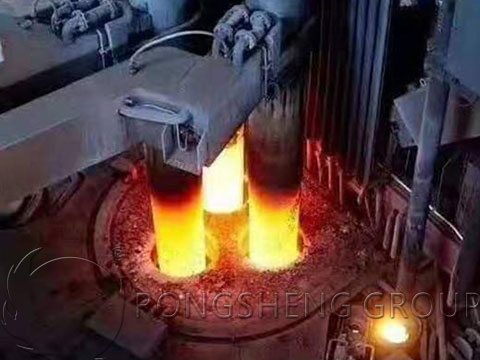
Graphite electrode for Steelmaking Electric Arc Furnace
The steel-making electric arc furnace uses graphite electrodes as conductive materials and transfers heat energy to the charge through arc discharge to melt the charge. An ordinary electric arc furnace has three electrodes, each of which is composed of 3 to 4 electrodes connected together with a tapered joint. The electrode is clamped by the holder at the end of the cantilever. The cantilever and the soft bus connected to the power supply rise and fall together.
The heat during smelting is generated by the arc discharge between the electrode and the metal charge. The arc formed at the tip converts electrical energy into heat for smelting needs. Since most of it is in the furnace, it bears the radiant heat of the high-temperature furnace gas, the surface of the molten pool, the furnace wall, and the arc column at the electrode tip. The furnace gas washes the surface of the electrode and heats the electrode by convection heating. This heat transfer effect increases with the increase of furnace gas and material temperature and furnace gas volume.
It is precisely because of such a harsh working environment compared with other conductive materials, graphite materials have some excellent or irreplaceable characteristics under high-temperature conditions. Graphite electrodes can be used at relatively high temperatures. The sublimation temperature is 3650°C. It is a high-temperature conductive material that can withstand high temperatures. In actual use, there is no other material that can replace it. The strength of graphite increases as the temperature rises at high temperatures. Graphite has the lowest thermal expansion coefficient compared with other metals.
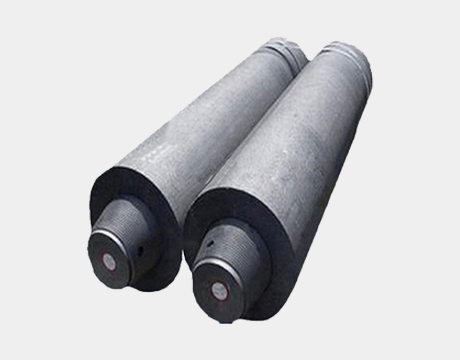
Current Consumption Status of Graphite Electrodes in Electric Arc Furnaces
Graphite electrodes are the central hub that converts electrical energy into heat. Its consumption mechanism includes high-temperature furnace gas oxidation consumption, slag erosion, and collapse and collapse caused by collapse and consumption. Among them, oxidation loss accounts for about 2/3 of the total consumption. The cost per ton of steel includes scrap, flux, depreciation, alloy, maintenance, and processing costs, among which processing costs account for about 30% of the cost of ton steel. Among the various expenditure items in the processing fee, the electrode cost accounts for about 30% to 40%. It can be seen that reducing electrode consumption is particularly important for reducing the cost of steel per ton.
As the carbon industry, a comprehensive evaluation method should be actively recommended, that is, the overall quality level and adaptability of graphite electrodes should be evaluated by the yield method. Use the electricity consumption method to compare the electrode quality and furnace conditions between batches. At the same time, other consumption in smelting must be considered.
Energy-saving and Consumption Reduction of Graphite Electrodes
In the case of variable manufacturing raw materials and production processes, it is necessary to conduct in-depth research and analysis on the consumption mechanism of electric furnace electrodes. The electric furnace steelmaking production has a theoretical basis for reducing the consumption of the electrode, the production becomes more rational, and the electric furnace steelmaking production is promoted to the direction of intensive development.
The energy-saving and cost control of graphite electrodes requires more than just exploring the consumption-reducing technology from the graphite electrode itself, such as water spray technology and surface coating technology. More attention should be paid to the overall steelmaking of ultra-high power electric arc furnaces, and the steelmaking process should be improved and optimized. So as to promote the innovation, quality improvement, energy-saving, and consumption reduction of graphite electrodes.