As a leading manufacturer of graphite electrodes, Rongsheng Manufacturer understands the critical role these components play in electric arc furnace (EAF) steelmaking. Steel companies worldwide depend on high-performance electrodes to ensure efficient melting, reduced energy consumption, and lower operational costs. This blog examines why graphite electrodes are indispensable for steel production, their key advantages, and the latest market trends influencing procurement decisions.
Why Steel Companies Rely on Graphite Electrodes
1. Essential for EAF Steelmaking
Graphite electrodes are the backbone of EAF steel production, conducting high currents to melt scrap metal at temperatures exceeding 3,000°C. Unlike traditional blast furnaces, EAFs offer:
-
Lower carbon emissions (up to 75% less CO₂ compared to integrated steel plants).
-
Faster production cycles (melting times reduced by ~30% with UHP electrodes).
-
Flexibility in raw materials (scrap-based steelmaking reduces reliance on iron ore).
2. Performance Advantages Over Alternatives
-
Higher Thermal Conductivity: Graphite electrodes withstand extreme heat without structural failure.
-
Lower Consumption Rates: UHP electrodes last 2–3x longer than copper alternatives, reducing replacement frequency.
-
Energy Efficiency: Optimized arc stability cuts power consumption by 30–50%.
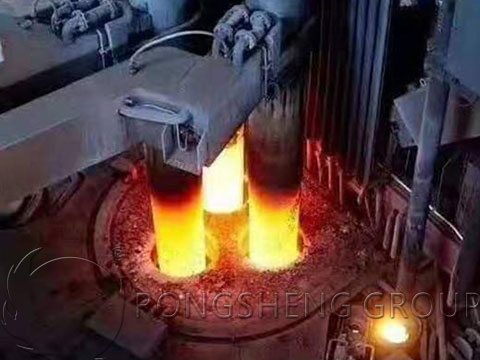
Key Factors Influencing Electrode Selection
1. Electrode Grades: HP vs. UHP
-
High Power (HP) Electrodes: Used in smaller or older furnaces, suitable for moderate current loads.
-
Ultra-High Power (UHP) Electrodes: Preferred for modern, high-capacity EAFs, offering superior durability and conductivity.
2. Quality & Material Composition
-
Needle Coke Purity: Low-sulfur (<0.5%) needle coke ensures stable performance.
-
Mechanical Strength: Flexural strength ≥11 MPa prevents breakage under thermal stress.
3. Supply Chain & Pricing Trends
-
Market Shifts: Recent exits by major producers (e.g., Resonac) have tightened supply, potentially driving prices up.
-
Regional Demand: Asia-Pacific dominates consumption (50% of global demand), led by China and India.
Future Trends in Graphite Electrodes for Steelmaking
1. Growing EAF Adoption
With global decarbonization efforts, EAF steel production is projected to grow at 5–7% annually, increasing electrode demand.
2. Technological Innovations
-
Oxidation-Resistant Coatings: Extend electrode lifespan in high-oxygen environments.
-
Smart Electrodes: Embedded sensors for real-time performance monitoring (emerging R&D focus).
3. Sustainability & Recycling
-
Scrap-Based Steelmaking: Rising scrap availability supports EAF growth, further boosting electrode needs.
-
Circular Economy Initiatives: Electrode recycling programs are gaining traction to reduce waste.
Conclusion
For steel companies, selecting the right graphite electrodes is crucial for cost efficiency, sustainability, and production reliability. As EAF adoption rises and supply dynamics shift, partnering with trusted manufacturers like Rongsheng Graphite Electrode Manufacturer ensures access to high-quality, competitively priced electrodes.
Contact us NOW for tailored electrode solutions that meet your steel production needs.