Yellow phosphorus is smelted in a submerged arc electric furnace, and the main raw materials are phosphate rock, coke, and silica. During production, these raw materials are pre-dried and crushed to a certain size. Next, the raw materials after drying and crushing enter the closed furnace from several discharge ports evenly distributed on the furnace cover according to a certain proportion. A chemical reaction occurs at a smelting temperature of 1400-1600°C to reduce elemental phosphorus. After cooling by water spray, the yellow phosphorus enters the collection device to obtain the liquid crude phosphorus product. Next, let’s learn about the application of Ф600mm UHP graphite electrodes in a 15MVA yellow phosphorus smelting furnace.
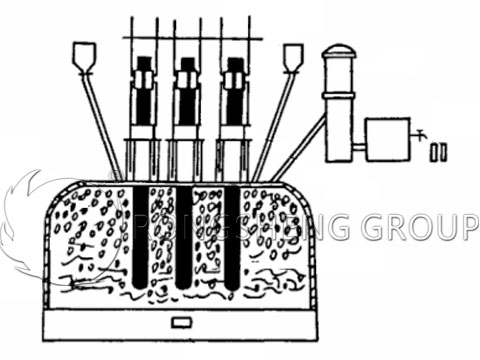
The Production Process of Graphite Electrode Smelting Yellow Phosphorus
Before opening the furnace for yellow phosphorus production, the three-phase electrode column is inserted into the furnace through the water seal, and each phase is connected by 5 electrodes to form a column. Then, the mixture is added at the same time from the discharge ports evenly distributed on the furnace cover. A 24kA current is passed through the electrode, and the charge is used as a heating element to heat itself. When the lower part of the furnace reaches about 1600°C, the charge melts and the current drops and the furnace body is divided into a molten layer, a semi-melted layer, and a raw material layer from bottom to top. As the smelting continues, the material level continues to drop in the process, and new materials continue to fill up.
In order to continuously melt the charge, the three-phase electrode must be continuously raised so that the electrode end is in contact with the falling semi-melt layer. Keep the current around 24kA at all times. The reduced yellow phosphorus continuously enters the collection device. When the water-sealed cover connected with the electrode holder hook rises to a certain height limit with the electrode, the yellow phosphorus gas escapes and catches fire. Open the ballast outlet to remove the molten ballast. The main component of molten slag is CaSiO2, which can be used as a building material. After the melting ballast is removed, the semi-melted layer and the raw material layer drop, the electrode and the water-sealed cover drop to the original height, and the current returns to 24kA. If the current is significantly lower than 24kA, it means that the charge resistance around the electrode end is too large, and it can be judged that the electrode is not long enough in the furnace. At this time, loosen the holder to lower the electrode or connect another electrode to the upper part. At this time, a short power outage is required. In this way, continuous smelting can continuously produce yellow phosphorus.
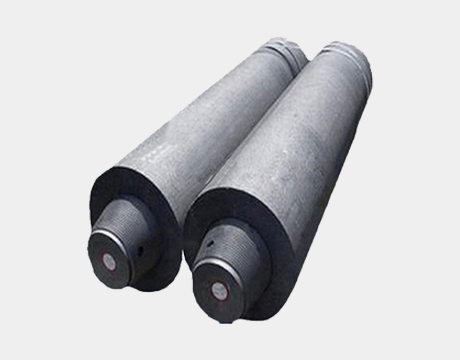
Comparison of the Quality of Graphite Electrode and Carbon Electrode in Yellow Phosphorus Smelting
Yellow phosphorus and industrial silicon are smelted by submerged arc smelting. One end of the electrode is buried in the material, and the current is transmitted to the material through the electrode, and the material is melted by the resistance heating of the material layer itself. Due to the higher resistance of the material, the current through the electrode is much lower than that of the steel-making electric arc furnace. Therefore, some yellow phosphorous manufacturers use a slightly larger carbon electrode to increase the cross-section and reduce the current density. The price of carbon electrodes is relatively cheap, and the production difficulty and cost are relatively low. Because it is a carbon product, the mechanical strength of the electrode is relatively high, and its electrical conductivity and mechanical strength are more in line with the requirements of yellow phosphorus production. However, the toughness of carbon products that have not been graphitized is not as good as graphitized products. It is used in furnaces that require high comprehensive performance of electrical conductivity and mechanical strength and has the disadvantages of high power consumption and electrode consumption. The poor current conductivity causes partial loss of electrical energy on the carbon electrode, resulting in thermal stress. In addition, the toughness is poor, and large pieces of material are dropped at the end during the smelting process. Whether the graphite electrode or carbon electrode should be used for yellow phosphorus smelting is determined by the yellow phosphorus smelting enterprise after measuring and calculating the furnace type, furnace capacity, thermodynamics, and electrode stress conditions.
Consumption of Ф600mm UHP Graphite Electrode in Yellow Phosphorus Smelting
Because it is a closed furnace type, the furnace is in a negative pressure state, and the oxidation consumption of the graphite electrode is very low. Its normal consumption is due to the small cracks and lumps caused by the thermal stress generated by the electrode end in the molten state of the charge for a long time. The falling block can be used as a reducing agent to participate in the reaction. The abnormal consumption is mainly caused by the collapse of the charge caused by coking, the longitudinal shearing force on the electrode column is very large, and the tensile strength of the joint with a relatively small cross-section is very high. In the application of Ф600mm UHP graphite electrode on the 15MVA yellow phosphorus smelting furnace, the working environment on the surface of the electrode used in the yellow phosphorus smelting furnace is relatively “calm”, not as “bad” as the steel-making electric arc furnace. The current density is not large, but if the conductivity between the electrodes is not good, such as the size and index do not match, connection operation problems and the existence of thermal resistance will cause stress. When the strength of the electrode root or the joint strength is low, the electrode will break when a large collapse occurs. Ф600mm UHP graphite electrodes have been used in batches, and the electrode unit consumption is equivalent to the level of imported UHP graphite electrodes, which fully meet the smelting requirements of 15MVA yellow phosphorus smelting furnace.
The Difference between Graphite Electrode Steelmaking and Yellow Phosphorus Smelting
As we all know, graphite electrodes are mostly used in steel-making electric arc furnaces. In addition, graphite electrodes are also used in the smelting of other minerals, such as the smelting of industrial silicon and yellow phosphorus. In their smelting, they mainly use the thermal effect of the graphite electrode to generate arcs to smelt metals and other materials. When steelmaking, the arc temperature of the electrode tip is above 3000℃; when smelting yellow phosphorus, the temperature of the electrode tip is about 1500℃. Due to the difference in smelting strength such as current density, open arc, and hidden arc in appearance, it seems that the two have different requirements for the quality of graphite electrodes, but in fact, the main performance requirements such as electrical conductivity and mechanical strength are basically the same. The only difference is that the smelting time per furnace of the electric arc furnace is short, and the current density on the graphite electrode is large. Although the continuity of yellow phosphorus smelting and production is good, and the current density is not as large as the steel-making electric arc furnace, the requirements for electrode conductivity are not low. The mechanical strength requirements of the electrodes, especially the joints, are higher, and sometimes even exceed the requirements of the electric arc furnace for the mechanical strength of graphite electrodes. This is objectively required due to the difference in the length of the series connection and the frequency of collapse. It is sufficient to connect 3 electrodes in series on a single-phase steel-making electric arc furnace, while a single-phase yellow phosphorus smelting furnace needs to connect 5 electrodes in series. Due to the different discharging methods, the collapse of the steel-making electric arc furnace is accidental, and the collapse of the yellow phosphorus smelting furnace may occur at any time. The replacement cost of the upper electrode of the steel-making electric arc furnace is relatively low, and the replacement cost is expensive once the electrode is broken in the yellow phosphorus smelting furnace.
The application of Ф600mm UHP graphite electrode in 15MVA yellow phosphorus smelting furnace has good results. At the same time, this is similar to the steelmaking industry in that the larger the transformer capacity, furnace capacity, and production capacity, the lower the power consumption and energy consumption of the furnace type, and the higher the requirements for the quality of the electrode. With the improvement of our yellow phosphorus smelting technology, we can analyze the electrical conductivity and force requirements of the electrode and the actual use of the electrode through the furnace type, so that we will have a clearer target for the production of graphite electrodes in the future. For more information about graphite electrodes, please contact us.