The measures to reduce the consumption of Graphite Electrodes in LF Furnaces are mainly included in the following aspects.
Choose Reasonable Power Supply Parameters
- 1) The power distribution system of the 50tLF furnace is divided into 11 gears, within the voltage range of 110 ~ 250V, each level increases by 15V. The 60tLF furnace power distribution system is also divided into 11 gears, with a voltage range of 170~270V, with an increase of 10 V for each level.
- 2) Optimize the power distribution process. Use appropriate arc voltage and current values to maintain the stability of the arc, reduce the change and impact of the electromagnetic force, and optimize the power distribution process. When the 50t LF furnace slags, the given power is selected as 85%, and the 1~3 gears are used. When raising the temperature, select the given power to be 95%, and use 9~11 gears. Select 70% of the given power during heat preservation, and use 5~7 gears. When the 60tLF furnace slags, the given power is 75%, and the 2~4 gears are used. When raising the temperature, select the given power as 85%, and use 8~10 gears. Select 50% of the given power during heat preservation, and use 5~7 gears.
Develop a Reasonable Slagging System
1) Choose a reasonable amount of slag. The slag thickness of the stable submerged arc should be ≥100mm (because the arc length is 70~90 mm), and the thickness of the lower slag layer of the converter is 30~50mm. Therefore, the thickness of the newly added slag should be at least 50~70 mm. The area of molten slag in the ladle is 3.5m2, the density of molten slag is 2.6g/cm3, and the amount of newly added slag should be 450 ~ 650 kg, including lime, fluorite, deoxidizer, etc.
2) Rapid foaming slag generation process. In order to accelerate the slagging rate in the early stage of refining, stabilize the argon stirring effect of molten steel, ensure a certain slag layer thickness and low-oxidizing slag, and maintain the stability of the arc, combined with the actual production, the secondary slagging system is determined to be adopted. A batch of slagging materials, operation under normal slag condition and temperature: the slag thickness is less than 70mm, and the temperature is within the required range of the steel grade. Lime 2/3, fluorite 1/2, and stir for 1 min under a large argon atmosphere. Make it evenly cover the surface of molten steel to prevent accumulation and lumps at the feeding port.
Addition of deoxidizer: According to the viscosity, color, and foaming degree of the top slag of the ladle, the oxidation of molten steel is judged. During the electrification process, the slag is adjusted with deoxidizers such as silicon calcium barium and calcium carbide. Among them, calcium carbide needs to be added in bulk, and after breaking the bag, it is deoxidized from the operation port by floating in. After the first sampling, two batches of slagging materials (lime, fluorite) should be added according to the slag situation. After sampling, add deoxidizers in batches according to the viscosity, color, and degree of foaming of the slag to adjust the slag to achieve continuous foaming.
Establish a Precise Bottom Blowing Argon Mode
The intelligent argon blowing system is used to optimize the argon blowing process, according to the refining purpose of different refining time periods. Choose different argon blowing modes, formulate standardized argon blowing operating procedures, and guide molten steel argon blowing operations. In order to achieve rapid slag melting and temperature increase, accelerate the slag circulation, maintain the stability of the molten steel level, reduce the electrode vibration amplitude, and extend the electrode life.
Design a New Type of Electrode Tightening Wrench
Eliminate the original fitter’s wrench, design and manufacture a new type of electrode tightening wrench, install fast-adjustable clamping teeth, increase the wrench arm, and ensure good electrode contact. Avoid excessive contact resistance, thereby reducing electrode consumption. At the same time, when there is a seam at the joint between the electrodes, the electrode may be broken at a high position, immediately use the electrode tightening wrench to re-tighten the electrode, so that the electrode can be reused.
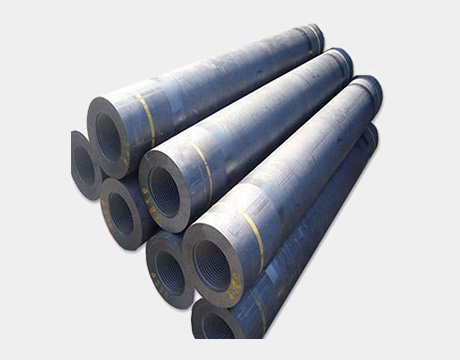
After the implementation of the above improvement measures for the LF furnace, the frequency of electrode disconnection is significantly reduced, the oxidation and spalling of the electrode and the corrosion of steel slag are significantly reduced, and the electrode consumption is greatly reduced. The consumption of refined electrodes is reduced to 0.22 kg/t steel. Ensure the stable operation of LF furnace equipment, improve the composition of molten steel, temperature qualification rate, and product quality.
1 thought on “How to Reduce the Consumption of Graphite Electrodes in LF Furnaces?”
Comments are closed.